What is a DC motor? - DC motor types, how they work, and how to control them
-
Automation
-
Health & wellness
-
Life environment
-
Automotive
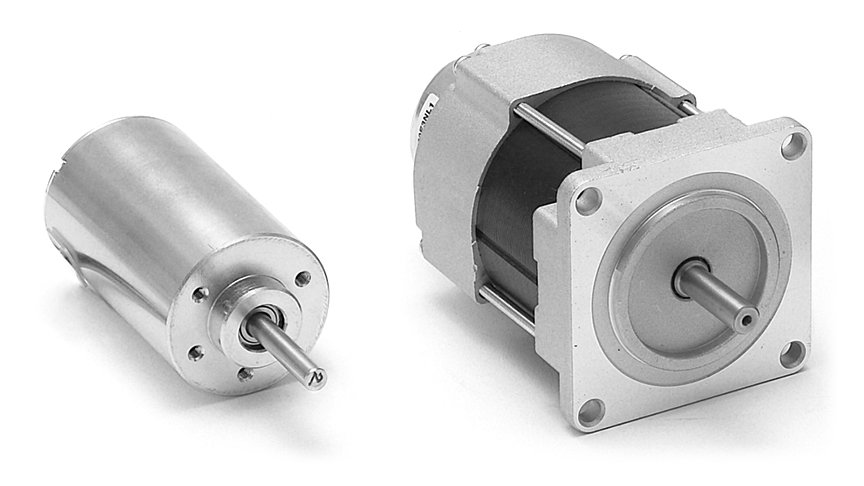
3 Jul. 2023
This article discusses the distinctions between DC motors and other types of electric motors, including the various types of DC motors and their respective functionalities and control mechanisms.
- DC motors are powered by direct current
- What distinguishes a DC motor from other types of electric motors
- DC motor type 1 - brushed DC motor
- How do brushed DC motors work?
- Drawback of brushed dc motors: electric noise and limited lifespan
- DC motor type 2 - brushless DC (BLDC) motor
- Outer-rotor and inner-rotor motors
- How do brushless DC motors work?
- Controlling brushless DC motor
- Advantages and disadvantages of the two types of DC motors
- Overcoming your problems with brushless DC motors
DC motors are powered by direct current
DC motors are specifically powered by direct current. They possess notable features such as the capability to rotate at high speeds and provide high starting torque. Due to these characteristics, they find extensive applications across various familiar settings. Generally, DC motors can be categorized into two main groups: brushed DC motors and brushless DC motors.
What distinguishes a DC motor from other types of electric motors
Generally, an electric motor converts electrical energy into mechanical energy, resulting in rotational motion and the accomplishment of work.
Types of electric motors
Electric motors can be broadly grouped into three categories based on their internal design and operational principles.
- DC motor (powered by direct current)
- AC motor (powered by alternating current)
- Stepper motor (a motor that rotates one step at a time in response to electrical pulses)
The table below describes the differences between DC motors and other types of electric motors.
Horizontal scrolling
DC motor with brush | Brushless DC motor | AC motor | Stepper motor | |
---|---|---|---|---|
Efficiency | Superior | Inferior | ||
Starting torque | Superior | Inferior | Inferior | |
Rotational speed | Higher depending on setting | 3,600rpm or less (bipolar, 60Hz) |
2,000rpm or less |
|
Possibility of missing steps or slipperiness | No | Slipperiness | Missing steps | |
Long lifetime | Depending on lifetime of brush | Yes | Yes | Yes |
Need driver circuit | No | Yes | No | Yes |
Control algorithm applied | Normally closed loop | Normally open loop | ||
Positioning control | Possible on servo motor | Possible on servo motor | Possible | |
Constant speed control | Superior | Best | Inferior | Superior |
The main features of DC motors are:
- Ability to operate at high speed
- High starting torque
- Motor speed and torque can be controlled by voltage
Features and applications of DC motors
DC motor type 1 - brushed DC motor
Brushed DC motors operate through the mechanical connection between their commutator and brushes. As the motor rotates, the brushes and commutator maintain constant contact. However, this continuous contact leads to wear and tear over time, which can eventually result in motor failure. Consequently, brushed DC motors have a shorter lifespan compared to brushless DC motors and require regular maintenance. Additionally, the constant contact between the brushes and commutator generates electrical and acoustic noise while the motor is in operation.
Furthermore, brushed DC motors can be classified into two subtypes: permanent magnet motors and electromagnet motors, each possessing distinct characteristics.
Permanent magnet brushed DC motor
A permanent magnet is a material that can maintain its magnetism for an extended time without relying on an external magnetic field or electrical current. When the stator of a brushed DC motor contains permanent magnets, it is referred to as a permanent magnet brushed DC motors.
Globally, this type of motor finds wide application in various fields, such as auxiliary automotive motors, as well as in model cars or boats. Furthermore, based on the rotor design, permanent magnet brushed DC motors can be further categorized into slotted, slotless and coreless motors.
Electromagnet brushed DC motor
An electromagnet is composed of a magnetic core and a surrounding coil of wire. It becomes magnetized only when an electric current is passed through the coil. Electromagnet brushed DC motors generate their magnetic flux with the electromagnet.
Electromagnet motors are classified into three types: shunt motors, series motors, or separately excited motors, depending on the connection between the rotor winding and field winding. These configurations are typically employed in mid-range to heavy-duty motors, offering varying levels of motor output.
How do brushed DC motors work?
Brushed DC motors feature wound coils in the rotor, surrounded by magnets contained in the stator. The two ends of a coil are connected to the commutator. In turn, the commutator is linked to electrodes known as brushes, enabling the flow of direct current electric power through the brushes and coil as long as the brushes and commutator maintain contact.
However, as the coil rotates, there comes a point where the brushes and commutator lose contact, interrupting the current flow in the coil. Despite this, the momentum of the coil propels it to keep rotating. As the consequence, the brushes and commutator come back into contact, reestablishing the current flow through a different coil.
This cycle switching of current flow enables the brushed DC motor to continue rotating. Brushed DC motors function on direct current, and their speed can be easily controlled by adjusting the applied voltage.
Brushed DC motor configuration
Drawback of brushed DC motors: electric noise and limited lifespan
As mentioned earlier, brushed DC motors possess a simple structure yet deliver high starting torque and can operate at high speeds. They are also ease of use and can function without a drive circuit if speed control is not necessary. However, brushed DC motors do have disadvantages to consider.
- Tendency to generate electrical and acoustic noise
- Relatively short lifespan and the need for regular maintenance
The generation of electrical and acoustic noise in brushed DC motors can be attributed to the continuous contact between the brushes and commutator during motor operation.
The limited lifespan of brushed DC motor is an important factor to consider. The constant contact between the brushes and commutator leads to gradual deterioration due to friction-induced wear. As the metal brushes wear down, their ability to effectively conduct electric power diminishes. Consequently, the motor’s performance is compromised. This is why the brushes and commutator are consumable parts, requiring regular inspection or replacement as part of maintenance.
DC motor type 2 - brushless DC (BLDC) motor
Brushless DC motors are a type of DC motor that do not require the brushes used in conventional brushed DC motors. They do not rely on these consumable commutator and brushes, resulting in longer lifespans and reduced maintenance needs. As a result, brushless DC motors are being increasingly used.
Another advantage of brushless DC motors is the elimination of electrical and acoustic noise caused by the contact between the brushes and the commutator. Consequently, brushless DC motors operate quietly.
Recent years have seen the development of a wide variety of mechanisms that use brushless DC motors, especially in the automotive industry as well as in home appliances, precision machinery, and equipment for medical applications.
Brushless DC motors that use permanent magnets in the rotor are called permanent magnet brushless DC motors (PM motors) or permanent-magnet synchronous motors. They can be further divided into the following types based on how the permanent magnet is fitted into the rotor.
- SPM motor: The permanent magnets are attached to the side surface of the rotor.
- IPM motor: The permanent magnets are embedded in the interior of the rotor.
The embedded magnets of IPM motors make them mechanically safer than SPM motors and capable of faster speeds.
SPM and IPM for inner-rotor brushless DC motors
Outer-rotor and inner-rotor motors
Brushless DC motors can be typically divided into outer-rotor and inner-rotor motors.
- Outer-rotor brushless DC motor
- An outer-rotor brushless DC motor feature coils located on the inside and magnets on the outside, resulting in the rotation of the outer circumference of the motor. While this configuration increases the moment of inertia of the rotor, it contributes to a stable and consistent rotation.
- Inner-rotor brushless DC motor
- An inner-rotor brushless DC motor utilizes magnets as the internal rotor and coils as the external stator. The advantage of this configuration is that the rotor has a low moment of inertia, enabling precise control.
How do brushless DC motors work?
Making an electric motor rotate requires that the direction of current flow through the motor windings (coils) is alternated in order to generate a rotating magnetic field. In the case of brushed DC motors, this is achieved through the mechanical action of brushes and commutator. Then how do brushless DC motors, which don’t have these parts, generate the rotating magnetic field, and turn?
Instead of a commutator and brushes, brushless DC motors use semiconductor switches. Brushless DC motors generally have three coils, with semiconductor switches connected to each of these. Turning the semiconductor switches on and off in the correct sequence alternates the current flow, which generates the rotating magnetic field that causes the motor to turn. Accordingly, the motors require a drive circuit to perform this sequencing. Furthermore, the semiconductor switches are switched by detecting the orientation of the permanent magnet rotor, using a magnetic sensor (typically a hall sensor).
Controlling brushless DC motor
Coil configuration and switching of brushless DC motor
The three coils of a brushless DC motor are connected together at one end, so by connecting the other end of one coil to the positive pole, and that of another coil to the negative pole, causes current to flow through both of these two coils. Two semiconductor switches are connected to each coil, one of which connects to the positive pole and the other to the negative pole. This gives a total of six switches, which, when turned on and off in the correct sequence, causes the motor to rotate. The timing of this switching is determined based on rotor orientation, which is detected by a hall sensor.
In other words, turning the semiconductor switches on and off in the correct sequence generates the rotating magnetic field that causes the brushless DC motor to rotate. And thus, a drive circuit is needed to perform this sequence of steps.
Excitation sequence of brushless DC motor
Configuration of brushless DC motor drive circuit
Drive circuits are made up of the following main elements.
- Rotational position sensor
- A hall sensor that detects the N and S poles of the rotor magnet.
- Position detection circuit
- A circuit that converts the signal from the hall sensor into a digital logic signal.
- Logic circuit
- Based on the signal from the rotor position detection sensor, this circuit outputs the sequencing that controls the direction of current flow through each coil.
- Pre-drive circuit
- A circuit that converts the sequencing signals into the signals for turning the semiconductor switches on and off.
- Semiconductor switches
- Typically, six semiconductor switches are used. These are turned on and off in accordance with the sequencing signals to achieve the current flow through the coils needed to make the motor rotate.
- Motor drive power supply
- Power supplies are required to provide the current flow through the motor coils and to power the logic and sensor circuits.
Diagram of brushless DC motor – sensor, control circuit and drive circuit
Brushless DC motors offer high performance without the issues of noise and limited lifespan that are commonly associated with brushed DC motors. While they do require a drive circuit, brushless DC motors overcome these challenges.
Advantages and disadvantages of the two types of DC motors
Brushed DC motors are currently the most commonly used because they are easy to miniaturize and provide good control of rotation together with high efficiency.
Brushless DC motors, on the other hand, benefit from long life, ease of maintenance, and low noise because they do not have the brushes and commutators, which are the downsides of brushed DC motors.
Features of brushed DC motors
- Advantages
-
- No need for a drive circuit when running at constant speed
- High-efficiency design
- Able to operate at high speed
- High startup torque
- Responsive and easy to use as speed and torque can be controlled by voltage
- Disadvantages
-
- Motor life is shortened by the need for brushes and a commutator, which are subject to wear
- The brushes generate both electrical and acoustic noise
Features of brushless DC motors
- Advantages
-
- Lack of brushes means long motor life
- High-efficiency design
- Stability of speed control
- Able to operate at high speed
- High startup torque
- Disadvantages
-
- A drive circuit is required
Overcoming your problems with brushless DC motors
ASPINA specializes in brushless DC motors among various types of DC motors. We not only develop standalone brushless DC motors but also provide system products that incorporate drive and control systems along with mechanical design. Our comprehensive support extends from prototyping to commercial production and after-sales service.
At ASPINA, we understand the diverse needs of different industries, applications, and customer products, as well as your specific production arrangements. That is why we offer customized solutions tailored to meet the specific functions and performance requirements of your project.
We are here to support not only customers who have clear requirements or specifications but also those who face challenges during the early stages of product development. Are you struggling with any of the following concerns?
- Motor selection
-
- Do you need advice or drive systems on motors even if you do not have detailed specifications or design drawings yet?
- Are you lacking in-house expertise to identify the best motor for your new product?
- Motor and associated component development
-
- Would you like to focus your resources on core technology while outsourcing drive systems and motor development?
- Do you want to save time and effort to avoid redesign of existing mechanical components when replacing the motor?
- Unique requirement
-
- Are you in need of a custom motor for your product after being declined by your usual vendor?
- Have you been unable to find a motor that provides the control you require, causing you to feel hopeless?
Need solutions to these problems? Get in touch with ASPINA now. We’re here to assist you.
List of the same series columns
- What is a brushless DC motor? What is the difference between brushless motor and brushed motor?
- Applications for blower motor
- What is a blower motor?
- Features and applications of DC motors
- Advantages of brushless DC motors over brushed DC motors
- Is this brushless motor cheap or expensive? - What factors determine its price?
- What is a geared brushless DC motor?
- How does an electronic speed controller for a brushless DC motor work? And what should you consider when you choose the right one?
- Small brushless motors
- What are the disadvantages of brushless DC motors? And how can they be overcome?
- Advantages of brushless DC motors: How they differ from brushed DC motors
- What is an actuator?
- Do brushless DC motors require a drive circuit? – Controlling brushless DC motors
- What is a stepper motor?
- What is an electric motor?
- How are stepper motors controlled? - Speed control of stepper motors
- How are DC motors controlled? - Speed control of DC motors
- Brushless DC motor applications: examples that demonstrate their features
- Stepper motor applications: Examples that demonstrate their features
- Motors designed for easy control: How do stepper motors work?
- What are the differences between brushed and brushless DC motors?
- What is a PSC motor
- What is a servo motor?
- What is a blower?
Contact us for more information
- New inquiry
- Prototype
- Upgrade
- Customization
- Your spec
- Literature
- Support
- Others