What is a brushless DC motor? What is the difference between brushless motor and brushed motor?
-
Automation
-
Health & wellness
-
Life environment
-
Automotive
-
Space
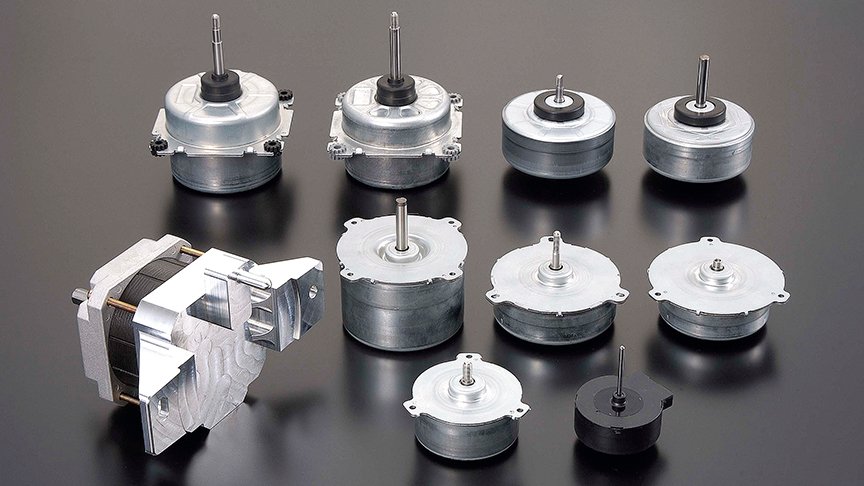
6 Dec. 2023
A brushless DC (BLDC) motor refers to a type of motor that lacks metal components (brushes) that contact the rotor to supply direct current to the coils. This article describes the mechanism, configuration, method of controlling rotation of brushless DC motors, and main applications for the motors, contrasting them with those of brushed motors.
Brushless DC motor operating principle
A brushless DC motor avoids the need for a commutator and brushes by having its permanent magnets in the rotor. The rotor’s rotation is sustained by detecting the position of its magnetic poles and adjusting the electric current flow through the coils accordingly. For this reason, a brushless DC motor requires a driver (an electronic drive circuit). Meanwhile, the rotor shaft position is detected using a hall effect sensor or other magnetic sensors (although motors capable of working without such a sensor also exist).
Hall effect sensors use the Hall effect to determine magnetic field strength. By converting this information into an electrical signal, the driver can detect the position of the permanent magnet (the orientation of its north and south poles) and switches the electric current flow through its coils in a way that keeps the motor shaft rotating.
Brushed DC motor (left) and brushless DC motor (inner-rotor type: right)
Components used in brushless DC motors
A brushless DC motor has a permanent magnet in the rotor and wound coils in the stator, whereas a brushed DC motor is the opposite, with wound coils in the rotor and a permanent magnet in the stator. In addition, while brushes and a commutator are essential for the rotation of a brushed DC motor, a brushless DC motor requires a drive circuit instead.
Brushless DC motor | Brushed DC motor | |
---|---|---|
Rotor | Permanent magnet | Wound laminated core |
Stator | Wound laminated core | Permanent magnet |
Control | Magnetic sensor and drive circuit | Brushes and commutator |
Motor controls for brushless and brushed DC motors
Brushless DC motor control
A three-phase brushless DC motor with an outer rotor, for instance, comprises three stator coils connected to six switches. The magnetic polarity (N or S) of the coils is determined by the on/off status of these switches, causing the rotor to rotate. In other words, the current flow is controlled to alternate the stator magnetic polarities, resulting in attractive and repulsive magnetic forces that drive the rotor to high speed.
The components of a control circuit for a brushless DC motor may include a magnetic polarity sensor to detect motor speed, a circuit to compare the actual motor speed with the reference speed, a circuit to calculate the required drive voltage, and a drive circuit to deliver this voltage.
Excitation sequence of 3-phase brushless DC motor
Brushed DC motor control
A brushed DC motor's rotation is governed by the interaction of brushes and a commutator. The stator houses the field magnet, and electrical current courses through the rotor coil. The brushes and commutator facilitate current flow from brush to commutator, inducing a magnetic force in the coil according to Fleming's left-hand rule, propelling rotor rotation. However, nearing 90°, the magnetic force shifts inward, threatening to halt rotation.
To counter this, the current is cut just before reaching 90°, allowing inertia to carry the rotor past that point. Subsequently, the current resumes in the opposite direction, propelling the rotor from 90° to the opposing 270°. The alternating current direction, reversing every 180° due to rotor rotation, sustains the motion.
Motor torque and speed are regulated by adjusting current in the coil, without altering its geometry, winding count, or the field magnet's flux density. Higher current results in increased torque and faster rotation.
Brushed DC motor configuration
Durability and noise issues
The physical contact between the brushes and commutator in a brushed DC motor means that these parts wear out over time. Additionally, the associated risks of electrical noise, sparking, and acoustic noise make this contact problematic at high speeds. Although brushed DC motors are cost-effective upfront, the requirement for maintenance, such as routine inspections or part replacements, has the potential to elevate their long-term costs.
In contrast, brushless DC motors do not experience the wear of the brushes and commutator or the electrical noise caused by brush contact. They are easier to control compared to brushed DC motors, utilizing a technique called sinewave drive to provide quiet operation with minimal vibration and electrical noise. This is why brushless DC motors are often selected for applications that demand long life and high efficiency.
Types of brushless DC motors
Brushless DC motors are broadly divided into those with an outer rotor and an inner rotor.
Outer rotor motor
Permanent magnets are located on the rotor which rotates around the outside of the stator coil windings, providing stability of rotation.
Inner rotor motor
Permanent magnets are on the rotor inside, with the stator coil windings outside. This configuration allows for precise control, similar to a brushed DC motor.
Brushless DC motors: Outer-rotor motor (left) and inner-rotor motor (right)
Brushless DC motors that use permanent magnets in the rotor are called permanent magnet brushless DC motors (PM motors) or permanent-magnet synchronous motors. They can be further divided into the following types based on how the permanent magnet is fitted into the rotor.
- SPM motor: The permanent magnets are attached to the side surface of the rotor.
- IPM motor: The permanent magnets are embedded in the interior of the rotor.
The embedded magnets of IPM motors make them mechanically safer than SPM motors and capable of faster speeds.
SPM and IPM for inner-rotor brushless DC motors
Applications for brushless DC motors
Due to their characteristics of small size, high output, low noise and vibration, and long life, brushless DC motors find applications in a wide range of uses.
- Air conditioners
- Home appliances
- Water heaters and burners
- Vending machines
- Freezer and chiller showcases
- Financial terminals (ATMs), change machines, currency exchange machines, ticket vending machines
- Clean rooms
- Optical products
- Printers
- Copiers
- Medical equipment
- Office equipment
- Laboratory analysis systems
- HVAC (Heating, Ventilation and Air Conditioning)
- Automotive
- Robotics
Overcoming your problems with brushless DC motors
At ASPINA, we specialize in brushless DC motors among various types of DC motors. In addition to developing standalone brushless DC motors, we provide system products that incorporate drive and control systems along with mechanical design. Our comprehensive support extends from prototyping to commercial production and after-sales service.
We understand the diverse needs of different industries, applications, and customer products, as well as specific manufacturing arrangements. That is why we offer customization solutions. Our solutions are tailored to meet the specific functions and performance requirements of each project.
We are here to support not only customers with clear requirements or specifications but also those who facing challenges during the early stages of product development.
Are you struggling with any of the following concerns?
- Motor selection
-
- Do you need advice or drive systems on motors even if you do not have detailed specifications or design drawings yet?
- Are you lacking in-house expertise to identify the best motor for your new product?
- Motor and associated component development
-
- Would you like to focus your resources on core technology while outsourcing drive systems and motor development?
- Do you want to save time and effort to avoid redesign of existing mechanical components when replacing the motor?
- Unique requirement
-
- Are you in need of a custom motor for your product after being declined by your usual vendor?
- Have you been unable to find a motor that provides the control you require, causing you to feel hopeless?
Need solutions to these problems? Contact ASPINA now. We are here to assist you.
List of the same series columns
- What is a DC motor? - DC motor types, how they work, and how to control them
- Applications for blower motor
- What is a blower motor?
- Features and applications of DC motors
- Advantages of brushless DC motors over brushed DC motors
- Is this brushless motor cheap or expensive? - What factors determine its price?
- What is a geared brushless DC motor?
- How does an electronic speed controller for a brushless DC motor work? And what should you consider when you choose the right one?
- Small brushless motors
- What are the disadvantages of brushless DC motors? And how can they be overcome?
- Advantages of brushless DC motors: How they differ from brushed DC motors
- What is an actuator?
- What is a stepper motor?
- What is an electric motor?
- How are stepper motors controlled? - Speed control of stepper motors
- How are DC motors controlled? - Speed control of DC motors
- Brushless DC motor applications: examples that demonstrate their features
- Stepper motor applications: Examples that demonstrate their features
- Motors designed for easy control: How do stepper motors work?
- What are the differences between brushed and brushless DC motors?
- What is a PSC motor
- What is a servo motor?
- What is a blower?
Related information
-
Accelerate product development: Rapid sampling and tailored solutions with ASPINA’s seat ventilation blowers
-
Zehnder revolutionizes indoor ventilation with ASPINA's DR-29312 motor
-
Comprehensive guide to medical device design
-
ASPINA's quiet medical-grade blower innovation revolutionizes CPAP therapy for sleep apnea sufferers
Contact us for more information
- New inquiry
- Prototype
- Upgrade
- Customization
- Your spec
- Literature
- Support
- Others