What are the disadvantages of brushless DC motors? And how can they be overcome?
-
Automation
-
Health & wellness
-
Life environment
-
Automotive
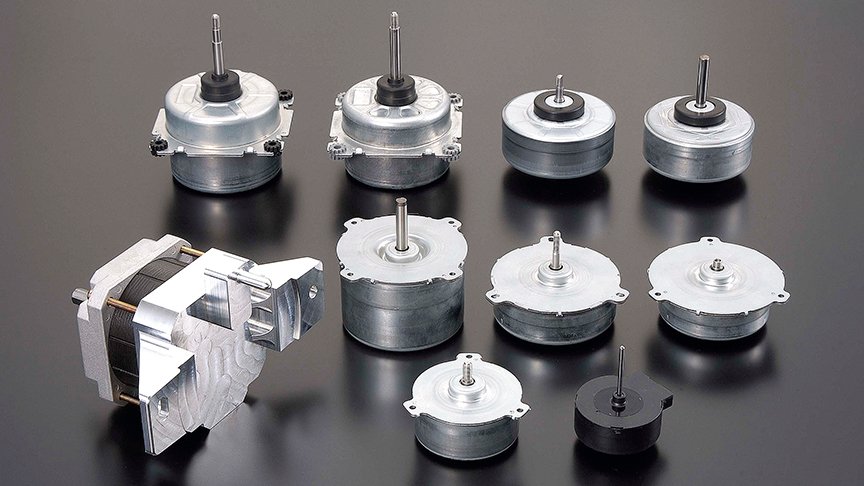
23 Aug. 2021
Modern industrial precision products need to be small, lightweight, highly reliable, efficient, and cost-competitive. Brushless DC motors achieve their longer life by doing away with the brushes and commutator required by brushed DC motors. When you choose a brushless DC motor rather than a brushed DC motor in your application, the choice must be made based on the performance and quality requirements of the product in actual applications. This article explains the disadvantages of brushless DC motors and what you would have to consider in your application.
- Brushless DC motors require a control circuit
- Brushless DC motors are available in a wide range of specifications to suit different applications
- Disadvantages of outer-rotor brushless DC motors
- Disadvantages of inner-rotor brushless DC motors
- Key considerations of using brushless DC motors in your application
Brushless DC motors require a control circuit
While connecting a power supply is all that you need to run a brushed DC motor, brushless DC motors cannot perform without a control circuit. Compared to a brushed DC motor, a brushless DC motor needs a more complex drive circuit.
The electric current through the coil of a brushless DC motor is switched by a semiconductor control circuit with an external sensor for detecting rotor position. When current flows in the coil such that the coil and magnet have the same magnetic polarity, the repulsive force between them causes the magnet to rotate away from the fixed coil. If they have opposite magnetic polarity, on the other hand, the force is attractive and control over the movement of the magnet is lost. Once the magnet has passed the coil pole in rotation, the direction of current flow needs to be reversed to maintain the repulsive force and keep the magnet rotating.
The control circuit uses an external magnetic sensor or similar device to detect the position of the north and south poles of the rotor. The phasing of the current is then controlled by alternately turning a transistor or other suitable switch on and off at the appropriate timings (rotor pole positions). If the current is controlled to have a square waveform that alternates at every 120°, for example, then torque is generated every 60°.
Brushless DC motors are available in a wide range of specifications to suit different applications
While electric motors come in many different types, brushed DC motors and stepper motors continue to be used widely. A wide variety of models are available from a wide range of vendors. Key considerations for motor selection include the size of the motor, its torque, and its speed in revolutions per minute.
Brushless DC motors, too, come in a range of variations, with the sensor and control circuit forming part of the basic design. Motor specifications are an important factor when selecting a brushless DC motor, just as a brushed DC motor. An additional factor that must be considered, however, is whether to choose an inner-rotor or outer-rotor configuration.
In addition, the position sensor used with the control circuit needs to be selected according to motor specifications such as the speed and direction of rotation. The choices might include a high-resolution optical encoder or resolver, or sensorless operation to eliminate the need for sensor maintenance.
Missing the opportunity to consider these questions can lead to the selection of a motor with higher-than-necessary performance and have a negative impact on material cost of the product you develop.
Disadvantages of outer-rotor brushless DC motors
A brushless DC motor with an outer-rotor configuration has a rotor embedded with magnets that rotates surrounding a stationary inner stator that contains the coil windings.
Having the rotor on the outside makes these motors larger in diameter than inner-rotor motors. As a result, they may not always be practical when there are constraints of space in the device where you install a motor.
A motor’s moment of inertia is proportional to rotor's weight, diameter, and length (or thickness). That is, outer-rotor brushless DC motors have a larger moment of inertia about the rotor and so tend to be slower to start because they require more energy to get turning. This is a disadvantage in applications where rapid startup is required.
Furthermore, having the rotating parts on the outside calls for additional protective features, including to protect against people touching the motor (resulting in burns or abrasions) and to prevent damage from dust or fluids.
Disadvantages of inner-rotor brushless DC motors
A brushless DC motor with an inner-rotor configuration has a rotor embedded with permanent magnets that rotates inside a surrounding stator that contains the coil windings.
As the smaller motor diameter means less inertia, the moment of inertia about the rotor is less than that of an outer-rotor motor. While this provides excellent characteristics for starting and stopping, it also means there is less available torque.
Furthermore, delivering the same torque characteristics in a smaller motor requires that a high magnetic flux density be achieved while still using small magnets. If the strength, durability, or adhesion of the magnets is inadequate, it risks their coming apart at high speed due to the centrifugal force in the rotor. This means that high-performance magnets and appropriate roto manufacturing processes are needed.
Key considerations of using brushless DC motors in your application
The important factors to consider when using brushless DC motors in your application are the type of control circuit to use and how much space the circuit will need. When replacing brushed with brushless DC motors, the choice should be based not only on criteria such as whether similar torque performance can be achieved, but also on whether the characteristics of the brushless DC motor are adequate in terms of the required functions when used together with the other associated equipment.
For example, the factors listed below are some of the ones to consider when prioritizing the issues that lie on your product design.
- Overall system and background tasks
- Motor control
- Diagnostics and analysis
- Communications
The disadvantages of brushless DC motors can be addressed by optimizing the design of the products in which they are used, including the motors themselves
In constrast of brushless motor's advantages, they also raise issues to be addressed such as the control circuit and configuration. It is crucial to understand the disadvantages that are inherent in how they work and to design products in a way that takes account of parts selection, the control circuit, and surrounding equipment.
To meet the needs of its customers, ASPINA develops and offers our products that are small, lightweight, and quiet. Please click the following links for more information about ASPINA drive systems and motors.
Case studies
Click the links below to know what ASPINA offers solutions with our products.
Resolving your problems with brushless DC motors
ASPINA supplies not only standalone brushless DC motors, but also system products that incorporate drive and control systems as well as mechanical design. These are backed by comprehensive support that extends from prototyping to commercial production and after-sales service.
ASPINA can offer solutions that are tailored to suit the functions and performance demanded by a diverse range of industries, applications, and customer products, as well as your particular production arrangements.
ASPINA supports not only customers who already know their requirements or specifications, but also those who are facing problems at early stages of development.
Do you struggle with the following concerns?
- Motor selection
-
- Don't have detailed specifications or design drawings yet, but need advice on motors?
- Don't have anyone in-house with expertise in motors and can't identify what sort of motor will work best for your new product?
- Motor and associated component development
-
- Need to focus your resources on core technology, and outsource drive systems and motor development?
- Need to save the time and effort of redesigning existing mechanical components when replacing your motor?
- Unique requirement
-
- Need a custom motor for your product, but been declined from your usual vendor?
- Can't find a motor that gives you the control you require, and about to give up hope?
Seeking answers to these problems? Contact ASPINA, we’re here to help.
List of the same series columns
- What is a brushless DC motor? What is the difference between brushless motor and brushed motor?
- What is a DC motor? - DC motor types, how they work, and how to control them
- Applications for blower motor
- What is a blower motor?
- Features and applications of DC motors
- Advantages of brushless DC motors over brushed DC motors
- Is this brushless motor cheap or expensive? - What factors determine its price?
- What is a geared brushless DC motor?
- How does an electronic speed controller for a brushless DC motor work? And what should you consider when you choose the right one?
- Small brushless motors
- Advantages of brushless DC motors: How they differ from brushed DC motors
- What is an actuator?
- Do brushless DC motors require a drive circuit? – Controlling brushless DC motors
- What is a stepper motor?
- What is an electric motor?
- How are stepper motors controlled? - Speed control of stepper motors
- How are DC motors controlled? - Speed control of DC motors
- Brushless DC motor applications: examples that demonstrate their features
- Stepper motor applications: Examples that demonstrate their features
- Motors designed for easy control: How do stepper motors work?
- What are the differences between brushed and brushless DC motors?
- What is a PSC motor
- What is a servo motor?
- What is a blower?
Contact us for more information
- New inquiry
- Prototype
- Upgrade
- Customization
- Your spec
- Literature
- Support
- Others