Casing structure innovation provides quiet and comfortable driving experience – Automotive seat ventilation blower motor
-
Automotive
-
Automotive seat ventilation system
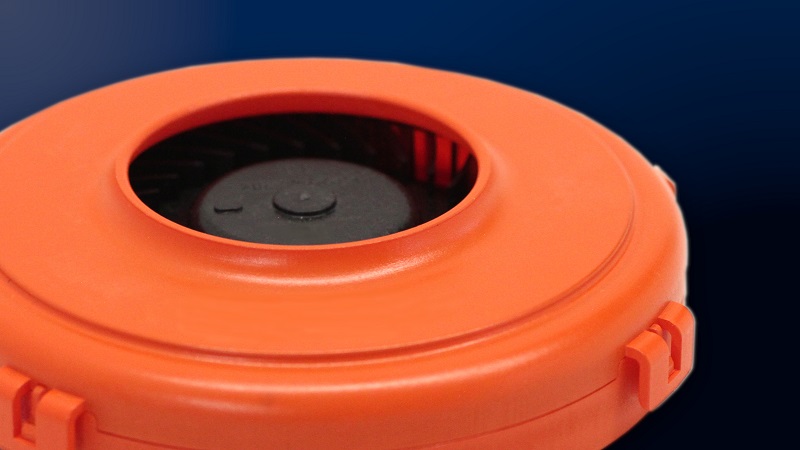
ASPINA’s optimal blower motor that aligns with the latest automotive seat ventilation system trends
“What is the best blower motor for a seat ventilation system?” This was the question ASPINA’s CM-BU (Car Mechatronics Business Unit) Research and Development Department set out to answer when they started developing their new product.
Until around 2018, most automotive seat air conditioning systems blew out warm or cold air from the seat surface, by using a peltier element temperature control mechanism attached to the end of a blower motor. Initially, these seat air conditioning systems were mainly installed in luxury cars, but gradually they began to be installed in middle class cars as well, leading to intensified cost competition. Around the same time, the need to reduce electricity consumption increased due to the shift to EVs. In response to these changes, the method of blowing out warm air from the seat was replaced by the heated seat which warms the seat surface with electric heating wires, and instead of blowing out cold air, ventilation by drawing in the cold air from the air conditioner became increasingly popular.
For a blower motor to draw air in from the seat surface, it must have enough static pressure to overcome its flow resistance. In particular, flow resistance increases when a passenger sits on the seat, so a blower motor with low static pressure would not be able to draw air in from the seat surface and ventilate, and thus would not function as a seat air conditioner. Looking at the trends in the automotive industry, we know it has become essential for vehicles to be quieter for improved passenger comfort. At the same time, the space available for installing blower motors is decreasing as seats become more multifunctional and slimmer. In other words, there is a need for a quieter, more low-profile and compact blower motor while also maintaining its air flow.
Most conventional blower motors for seat ventilation are the single outlet type, which ASPINA also manufactures. However, one time, when testing our conventional model mounted on a seat, the CM-BU Research and Development Department chief engineer noticed a slight noise. Although it was at a level that would not cause any problems as a product, he thought “we can do better”. And so, the R&D chief engineer and his team decided to improve their seat ventilation blower motor, with the concept of making it quieter, more low-profile, more compact, while maintaining flow rate.
The blower casing’s back outlet structure and diffuser enables a low noise, low-profile, compact product, with high static pressure
What the R&D chief engineer and his team developed, was a blower motor that reduces noise by blowing air out the back of the casing and has boosted static pressure from an added diffuser.
ASPINA's back outlet blower motor for automotive seat ventilation blows air out the back of the casing
After examining conventional products, the team found that the loudest noise generated by the blower motor was the wind noise emitted from the blower outlet. The most effective shape of the casing to reduce this wind noise, while simultaneously making the unit low-profile and compact, was to blow air out from the back. Noise measurements of this back outlet blower motor showed that it reduced noise by 7dB without passengers and 9dB with passengers, compared to the conventional single outlet type.
Noise measurement comparison of ASPINA's conventional and back outlet blower motor
However, although this back outlet structure is effective in reducing noise, it has the disadvantage that it does not generate enough static pressure due to P-Q characteristics, compared to the conventional sirocco fan + side outlet casing products. As mentioned above, static pressure is essential to draw air from the seat surface. The R&D team decided to make improvements to boost static pressure.
According to Bernoulli's principle, the energy of a fluid in steady flow can be expressed by 1. speed, 2. pressure, and 3. height, the sum of which is constant. In other words, the key to increasing the static pressure of a blower motor, is to slow down the air flow. Based on this principle, a diffuser was added to the casing to slow down the air that blows out. By converting part of the air speed into pressure, the R&D chief engineer and his team was able to close in on to the ideal P-Q characteristics for seat ventilation systems.
P-Q characteristics of a blower with and without a diffuser
Low noise and low profile are no longer mutually exclusive while maintaining output due to ASPINA engineers’ market awareness and trial-and-error
When developing this blower motor, it was difficult to achieve low noise, low-profile, and compactness; all the while maintaining output. Generally speaking, there is a trade-off between low noise and small size and is difficult to achieve both. As EVs are expected to become increasingly popular, and since they carry a large number of batteries in the chassis section, the space under the seats tend to become smaller. Furthermore, seats have become multifunctional in recent years to improve passenger comfort, so the internal structure has become more complex, thus again, space within the seat is limited. ASPINA’s R&D team knew that it was essential for automotive OEMs and tier-1 companies that the blower motors they use are low-profile and compact.
To solve this challenging issue, the R&D team studied various fan and blower structures in the market for clues. For example, the mainstream single outlet type has a large blower outlet area and can lower noise levels, but was difficult to make the blower itself low-profile and compact. The dual outlet type on the other hand has limitations to the direction of the blower outlet, and would also make internal seat structure complicated with its ducts, which is not suitable for seats with limited space.
Front picture of a single outlet (left) and dual outlet (right) blower motor
ASPINA’s blower motor for seat ventilation systems was developed to achieve low noise with its back outlet structure, boosted pressure from its diffuser, and a low-profile, compact casing. All of this was made possible in a single product by thorough examination of various design parameters. As a result, our back outlet blower motors for seat ventilation systems are 15mm smaller in size compared to our conventional single outlet product, while maintaining static pressure.
Size comparison of ASPINA's conventional and back outlet blower motor
ASPINA’s back outlet blower motor contributes to the growing EV market and allows for further improvements to vehicle cabin comfort
Our blower motor for automotive seat ventilation systems is low-profile and compact, yet quieter than ASPINA's conventional products and those of other companies; one of the quietest of its size. In other words, it can be installed in seats with limited space, and brings a quiet and comfortable driving experience for passengers while providing excellent seat cooling. Furthermore, blower motor casings are often made by resin molding, and the back outlet structure of this product has advantages compared to other shapes, in terms of securing the rigidity of the casing, mold effectiveness, and cost.
EV sales are expected to grow in the future. Unlike conventional ICEs (Internal Combustion Engine cars), EVs are driven by motors and are quiet to begin with, so the demand for quietness is expected to increase. ASPINA’s innovative blower motor matches this trend and is on the cutting edge of cabin comfort technology. Production is being increased as ASPINA anticipates to meet the demand and support increased vehicle instillations.
Related information
-
Seat ventilation blower
DRF-29A306 EV-TProducts & services
-
Compact and high performance seat ventilation systems made possible with back outlet blower motor
Case studies
-
Sleeve bearing development surpasses automotive industry standards – Automotive seat ventilation blower motor
Technologies
-
Accelerate product development: Rapid sampling and tailored solutions with ASPINA’s seat ventilation blowers
Case studies
Exhibition information
-
5 Feb. 2025
-
21 Oct. 2024